Parlementaire Monitor
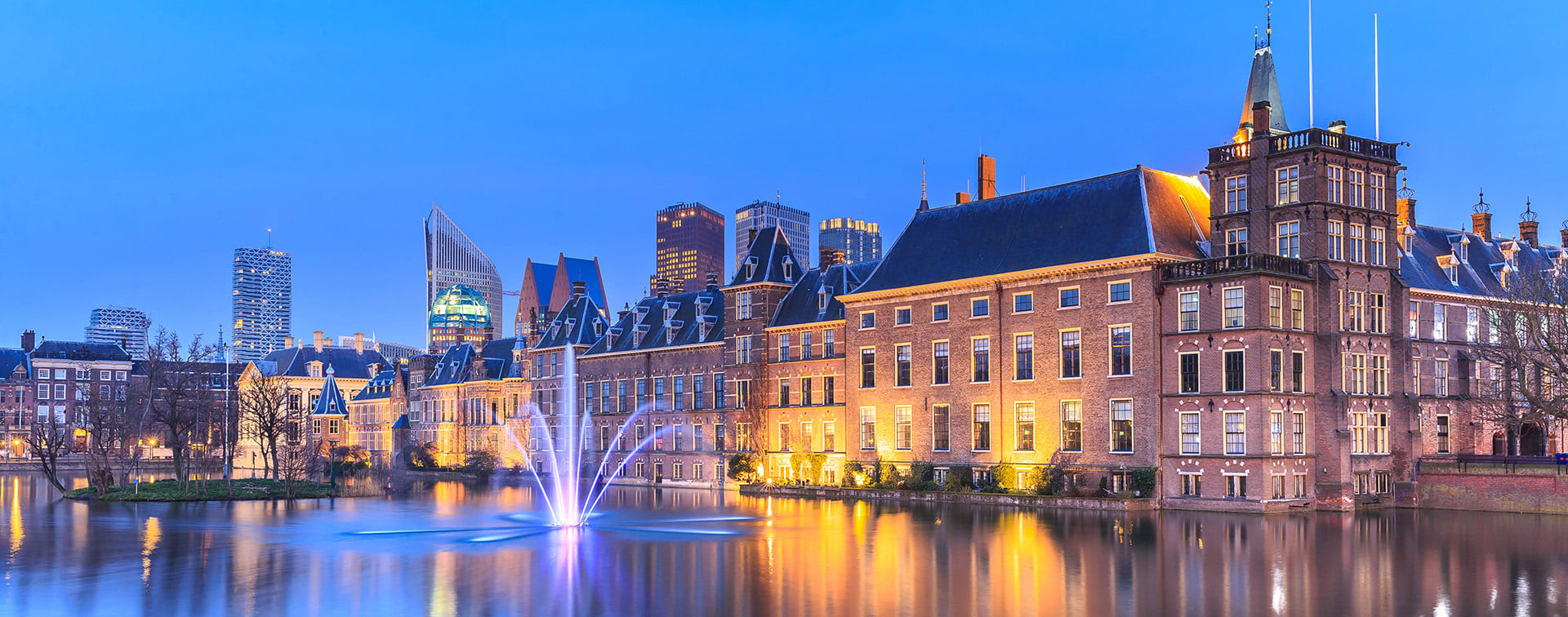
Toegang tot het gehele parlementaire besluitvormingsproces
Altijd op de hoogte van de laatste parlementaire ontwikkelingen met de Parlementaire Monitor.
Parlementaire besluitvorming
De Parlementaire Monitor geeft duidelijk aan in welke fase de besluitvorming verkeert. Kunt u nog invloed uitoefenen of is het nog slechts een kwestie van afhameren in de Eerste Kamer? Ook wordt aangegeven wie de belangrijkste stakeholders zijn en hoe u deze kunt bereiken. Zo kunt u tijdig en doeltreffend inspelen op nieuwe wet- en regelgeving.
Door informatie te bundelen in dossiers geeft de Parlementaire Monitor direct antwoord op de belangrijkste vragen. Deze hoeft u niet uit een groot aantal losse documenten bij elkaar te lezen.
Altijd inzicht in actuele wetgeving
De Parlementaire Monitor wordt 24 uur per dag, 7 dagen per week geactualiseerd en kan geraadpleegd worden op alle devices.
-
-Binnen de Parlementaire Monitor is het ook mogelijk (persoonlijke) topics in te stellen.
-
-Aan ieder topic kunt u een e-mailalert koppelen, zodat u doorlopend op de hoogte wordt gehouden van informatie die voor úw organisatie van belang is.
-
-Daarnaast is het mogelijk om uw achterban - al dan niet geautomatiseerd - op de hoogte te houden middels vanuit de Parlementaire Monitor verstuurde nieuwsbrieven. Het uiterlijk hiervan kan uiteraard worden aangepast aan uw behoeften.